Injection molding vs thermoforming: which manufacturing process is right for you?
- Posted on
- Posted in Arts & Crafts, Food, Home decor
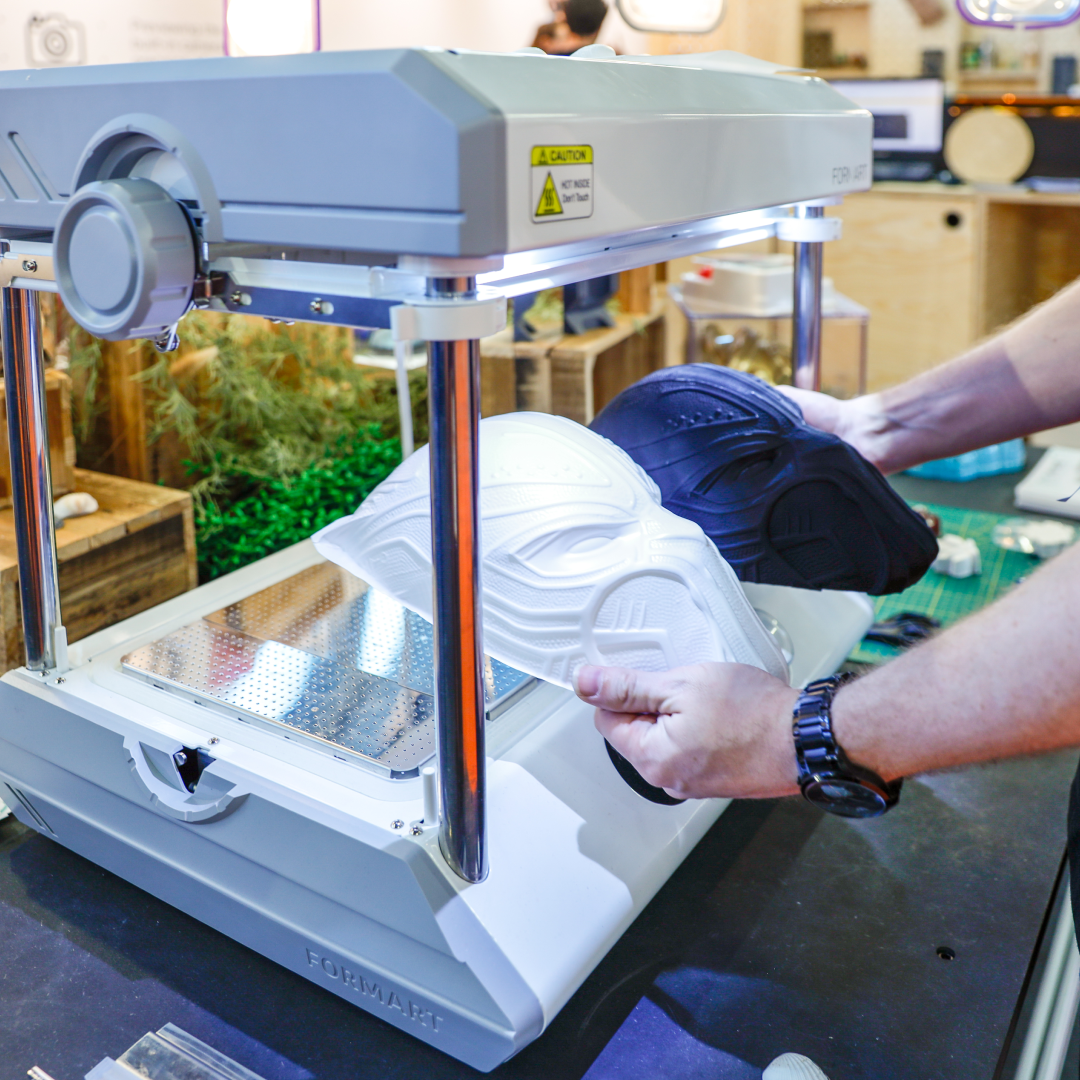
Compare thermoforming vs injection molding to find the best plastic forming method for your project. Learn the pros, cons, and when to use vacuum forming in manufacturing.
In today’s fast-moving manufacturing landscape, selecting the right plastic forming process is crucial to product success. Two of the most widely used techniques are thermoforming and injection molding. While both offer effective solutions for creating plastic components, each method comes with distinct advantages, limitations, and ideal use cases.
This guide compares injection molding vs thermoforming, outlines the differences between the two, and helps you decide which method suits your project requirements best.
What is thermoforming?
Thermoforming is a plastic manufacturing technique where a thermoplastic sheet is heated until it is pliable, then shaped over a mold using vacuum or pressure. After forming, excess material is trimmed away to reveal the finished part.
One of the most popular subtypes of this process is vacuum forming, where suction is used to pull the heated plastic tightly onto the mold surface. This technique is widely used across industries including packaging, automotive, retail display, and more.
Thermoforming is especially suitable for producing low to medium volumes of large or relatively simple components (e.g. packaging and automotive components), thanks to lower tooling costs and quick turnaround times.
Advantages of thermoforming
- Low-cost tooling: Thermoforming molds are typically made from aluminum or composites, making them significantly cheaper than injection mold tools.
- Faster prototyping: Ideal for short lead times, especially when testing form and fit before full-scale production.
- Design flexibility: Thermoforming supports a wide range of colors, surface textures, and post-processing techniques (e.g. painting, printing).
- Easy modifications: Design changes can be implemented quickly and affordably.
- Great for smaller runs: Typically used for runs of 250 to 3,000 parts, making it ideal for prototyping, niche products, and bespoke solutions.
Disadvantages of thermoforming
- Not suitable for high volumes: Producing large quantities can be inefficient compared to other methods like injection molding.
- Often needs manual finishing: Additional trimming or assembly steps may add to labour costs.
- Greater material waste: Some sheet material may be lost during trimming, especially in more intricate designs.
What is injection molding?
Injection molding is a high-precision process where melted plastic pellets are injected under pressure into a steel or aluminum mold. Once cooled, the mold opens to release the fully formed component.
This method is ideal for high-volume production of detailed, consistent plastic parts and is used extensively in the automotive, medical, packaging, and consumer electronics sectors.
Advantages of injection molding
- Scalable for mass production: Can produce thousands or millions of identical parts efficiently using multi-cavity molds.
- High precision and complexity: Suitable for producing intricate features and tight tolerances.
- Automation-ready: Highly automated process reduces human error and speeds up production.
- Lower per-unit cost at scale: Once the tooling is in place, each part costs significantly less.
- Low waste: The process generates minimal scrap, making it more material-efficient.
Disadvantages of injection molding
- High initial investment: molds are costly and typically made of hardened steel, making the upfront costs significant.
- Longer lead times: Designing and fabricating molds can take 12-24 weeks.
- Less economical for small batches: High setup costs make it less viable for low-volume runs.
Key differences between thermoforming and injection molding
Injection molding |
Thermoforming |
|
Tooling costs |
High (steel molds) |
Low (aluminum or composite molds) |
Production volume |
Best for high-volume production |
Ideal for small to medium batch runs |
Part complexity |
Supports intricate and precision parts |
Better for simpler or larger shapes |
Lead time |
12–24 weeks |
6–12 weeks |
Material efficiency |
Minimal waste |
May involve more off-cuts and scrap |
Flexibility |
Suited to fixed designs and long-term runs |
Easy to modify and prototype quickly |
When to choose thermoforming or vacuum forming
Opt for thermoforming when your project involves:
- Larger components such as panels, trays, or housings
- Low to mid-volume production (up to around 3,000 units)
- Simpler geometries that don’t require complex internal structures
- Quick prototyping needs for packaging, point-of-sale displays, or vehicle parts
Vacuum forming, in particular, is ideal for creating lightweight, rigid plastic items with excellent visual presentation at a low cost.
When to choose injection molding
Go with injection molding if your project requires:
- High precision and consistency
- Small, detailed parts such as gears, caps, enclosures, and fasteners
- Mass production, where the per-unit cost must be minimized
- Complex designs that involve varying wall thicknesses or undercuts
Conclusion
Both thermoforming (including vacuum forming) and injection molding are valuable plastic manufacturing processes, but the right one depends on your project’s scope, complexity, and budget.
If you require low-volume runs, large parts, or fast turnaround times, thermoforming may be your best option. For high-volume, detailed components, injection molding provides the speed and repeatability needed at scale.
Looking for an accessible, flexible thermoforming solution? The MY YARD desktop vacuum forming machines are perfect for quick prototyping and small-batch manufacturing.
Explore our range to see how vacuum forming can enhance your product development process.