6 types of plastic molding
- Posted on
- Posted in Arts & Crafts, Food, Home decor
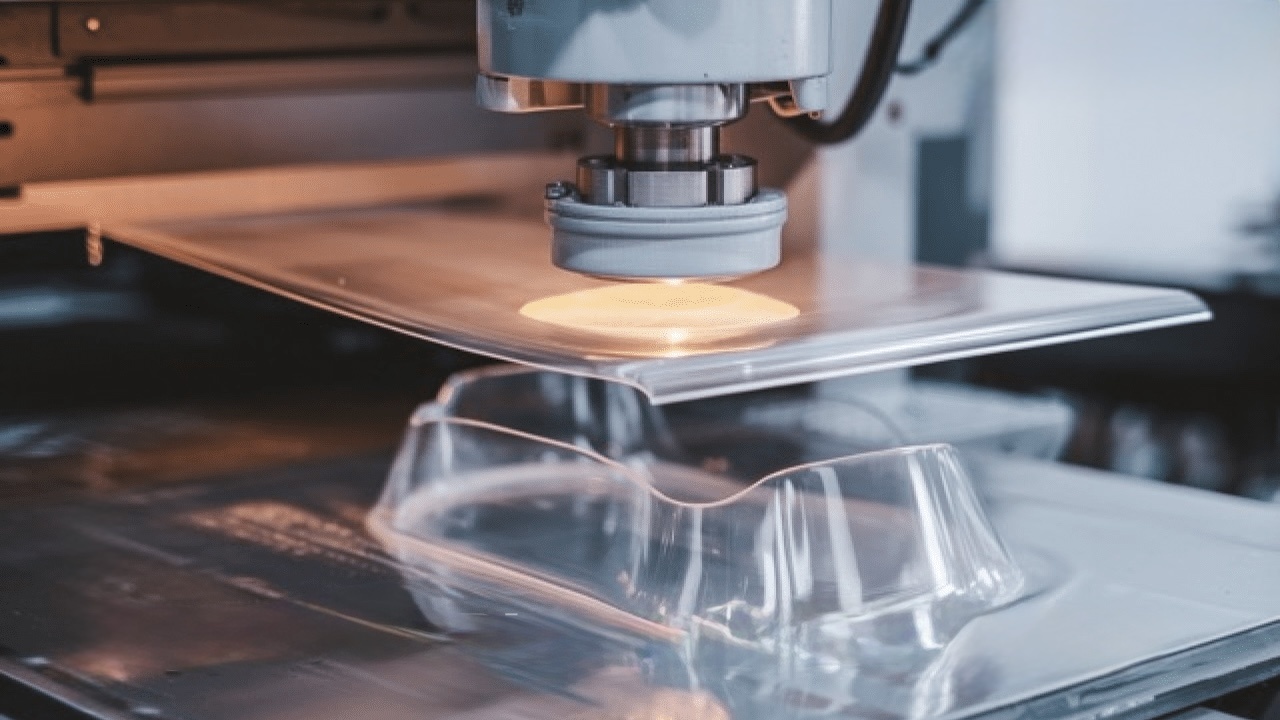
There are a lot of plastic molding techniques, each with its own strengths and weaknesses. In this guide we will introduce six types of plastic molding, from injection molding to vacuum forming. Find the right solution for your manufacturing needs.
Plastic molding is a fundamental manufacturing process that transforms raw plastic materials into a wide variety of useful products. From everyday household items to precision automotive components, the choice of molding method can significantly influence the final product’s performance and cost. In this comprehensive guide, we examine the key plastic molding techniques, including vacuum forming, and explore their benefits, applications, and suitability across different industries.
Injection molding
Injection molding is one of the most widely used plastic forming processes, ideal for producing high volumes of precision components. In this method, plastic pellets are melted and injected into a custom mold cavity. Once cooled and solidified, the part takes on its final shape.
Renowned for its accuracy and repeatability, injection molding is suitable for intricate designs and tight tolerances. It supports a broad range of plastics, including thermosetting and thermoplastic materials, and is commonly used in the automotive, medical, and electronics sectors. This technique is often used for products such as car parts, medical instruments, and plastic bottle caps.
Blow molding
Blow molding is used to manufacture hollow plastic components with uniform wall thickness. During the process, a molten plastic tube is extruded and expanded by blowing air inside, forcing the material against the walls of a mold.
Ideal for producing bottles, containers, and fuel tanks, blow molding is fast and cost-effective. It is widely used in the packaging, pharmaceutical, and personal care industries, particularly for items made from HDPE or polypropylene.
Compression molding
Compression molding involves placing heated plastic material into a mold cavity, which is then compressed into shape. This technique is particularly effective for producing strong, durable parts with thick profiles.
Commonly used in the automotive sector for items such as bumpers and electrical insulators, compression molding also lends itself to industrial applications like body armor and large appliance parts. It accommodates materials such as fiberglass-reinforced resins and other advanced composites.
Extrusion molding
Extrusion molding continuously pushes molten plastic through a die to create long products with a consistent cross-sectional profile. This method is well-suited for manufacturing pipes, tubes, and custom profiles.
Used extensively in the construction and electrical industries, extrusion molding enables the production of items such as PVC piping, plastic sheeting, and cable insulation.
Rotational molding (Rotomolding)
Rotational molding is ideal for producing large, hollow plastic objects. A measured amount of powdered plastic is placed in a mold, which is then heated and rotated along two axes. The melted plastic coats the inside of the mold evenly, creating a seamless product.
Rotomolding is known for its low-waste process and ability to produce durable items with even wall thickness. Typical applications include water tanks, playground equipment, and outdoor furniture.
Thermoforming
Thermoforming is a popular method in plastic forming, especially for thin sheet materials. A plastic sheet is heated until pliable, then shaped over a mold using vacuum or pressure. Once formed, the part is cooled and trimmed.
A key subtype of this technique is vacuum forming, a cost-effective and highly versatile process where a heated plastic sheet is drawn tightly over a mold using vacuum suction. Vacuum forming is particularly valued for its accuracy in reproducing shallow and detailed molds.
Thermoforming (and vacuum forming) are widely used in sectors such as:
- Custom packaging
- Automotive panels and interior trims
- Point-of-sale displays
- Chocolate molds and resin castings
- Clamshell and blister packaging
Because of its relatively low tooling costs, vacuum forming is ideal for both prototyping and small-to-medium production runs. It supports a wide range of plastic types and allows for a high degree of design flexibility. This makes it a preferred method for businesses seeking affordable, high-quality manufacturing solutions.
Choosing the right plastic molding technique
Each plastic molding process offers distinct advantages depending on your design complexity, production volume, and material requirements. Whether you're manufacturing lightweight packaging or large, structural components, selecting the right forming method can greatly improve efficiency and product quality.
Discover desktop vacuum forming with MY YARD
Ready to bring your ideas to life? MY YARD’s all-in-one vacuum formers make it simple to create professional-grade molds and products right from your workshop. Perfect for makers, hobbyists, and small manufacturers, our vacuum forming machines offer:
- Built-in vacuum pumps and heating
- Easy operation and compact desktop design
- Compatibility with various plastic sheets
- Rapid prototyping
- Precise, detailed forming
Whether you're experimenting with packaging, resin casting, or creating custom parts, MY YARD provides an affordable, scalable vacuum forming solution for businesses and creatives.
Take your plastic molding to the next level. Explore the benefits of vacuum forming with MY YARD today!